The range of applications using power electronic converters have dramatically increased in the last few decades. While initially, power electronic converters were mainly used in industrial applications, these are now widely propagated in household appliances. These products range from low voltage, low current applications such as DC-DC power supplies, small battery chargers, and USB-operated devices to high voltage, high current applications like inverters, solar power converters, and motor drives. An electrical designer can choose low voltage, high current topology or high voltage, low current topology for their application.
For our discussion here, we elaborate on the challenges and the solutions available to design a high voltage converter.
The Purpose of High Voltage Designs
With high voltage energy transmission, the amount of power loss can be minimized. At a high voltage, the current is low. With low current, the conduction loss is low. This implies that, with low conduction loss, energy loss is minimized, leading to better thermal management.
The primary source of electrical power is grid. Depending on the applications, the high voltage AC grid is converted to the system-specific AC/DC voltages. In most countries, AC-DC converters above 65W should maintain a unity power factor to reduce the reactive power from the grid. The unity power factor can be achieved by shaping the input current to a sinusoidal form in sync with the grid voltage, which can be realized by the topology where the AC voltage is rectified and boosted to a DC ranging from 400V – 800V DC.
The availability of a wide range of high boost ratio converters and resonant converters has made our task relatively easier today. Systems like solar inverters, online UPS, and other storage-based systems may have low voltage batteries as storage elements. Generation of an AC voltage of 230V/240V requires a DC bus of at least 400V, where the low voltage DC is boosted to a high voltage DC and then converted into the required AC by an inverter. With converters, the three-phase systems can be easily generated from a single high voltage DC bus of 600V-800V.
High Voltage Design Challenges and Solutions
With high voltage, the risk and challenges of associated circuity and design also increases. But with the right approach and careful design practices, we can achieve a foolproof system.
Device Selection
Devices or components are the major building blocks of any system. Once the appropriate building blocks are selected, the system is no longer prone to failure. But in the case of high voltage systems, the availability of such devices is one of the major concerns. 400V DC designs are easier to manage due to the wide availability of silicon devices in the range of 650V-800V. For 800V DC designs, limitations arise due to the narrow portfolio of 1000V silicon devices. With the development of 1000V-1200V Silicon carbide devices and GaN devices, designing a converter with 800V DC has become easier; however, the cost is higher, compared to a 400V DC designs.
One of the major components of any power converter is the capacitor. Aluminum electrolytic capacitors above 450V rating are expensive and hard to find. Above 400V design requires a series and parallel capacitors to achieve the required capacitance and voltage rating. This makes the DC link bulky, heavy, costly, and prone to losses. For high voltage capacitors, the leakage current and ESR will be higher; thus, the losses are also higher. Series connection of capacitors requires balancing resistors to avoid the voltage imbalance, which adds losses to the system.
Instead of series and parallel connection of Aluminum electrolytic capacitors, a combination of Aluminum electrolytic with film capacitors could be an effective solution. With proper circuit analysis, the ripple current distribution can be found for both Aluminum electrolytic and film capacitors, and appropriate combination can be used to reduce the total ESR losses.
While selecting high voltage devices, proper voltage derating factors must be considered. An approximate voltage derating factor of 0.8 – 0.85 can be considered for MOSFETs and diodes, and for capacitors, maximum of 0.9 can be considered.
Creepage, Clearance and Isolation Requirements
High voltage systems require extensive care in component placement while preparing the PCB layout. As voltage increases, the creepage and clearance requirement must also be improved to avoid isolation breakdown. Further, higher creepage and clearance boost the overall size of the PCB and the system.
In converters, isolation is offered by transformers where the primary and secondary are physically away from each other. While designing the transformer, care should be taken to decide winding sequences, insulating materials, and winding terminations. With higher working voltage and isolation requirements, the transformer’s size will increase, leading to increased core losses. Conduction losses also increase due to an increase in winding length.
Another segment to be considered for high voltage systems is connectors, cables, and enclosures. The wrong selection of these may cause isolation breakdown, electric shock, and fire. With high voltage systems, the connector size and cable insulation will increase. This will add up costs and dimensions. Similarly, enclosures and casings also need higher isolation, which will increase the product’s overall size.
Creepage and clearance values recommended by standards should be rigorously followed while designing the high voltage PCB. The designer must prepare the isolation rules/constraints to follow the required clearance/creepage for placement and routing. Slots and cuts can be provided in the PCB to increase the creepage distance between the high voltage components or traces wherever required.
PCB Design
For high voltage converters, creepage and clearance play a significant role in the PCB design. Higher creepage and clearance requirements make the overall PCB size large, leading to manufacturability and assembly issues. Â Components on big PCBs could fail during transportation due to vibrations. Also, PCB tends to bend where weighted components like capacitors, inductors, transformers, and heatsinks are mounted. This may lead to breakage or failure of SMD components and trace cuts on the PCB. However, with appropriate mounting arrangements, mechanical supports, and proper PCB design, such failures can be avoided in larger PCB-based designs.
For high voltage systems, the dielectric material used in the PCB should satisfy the isolation requirements between the layers. The dielectric materials should be chosen as per standards, and materials with the right flammability class should be used for manufacturing.
Moisture and dust contribute to an increase in the PCB leakage current over time. Moisture and dust accumulation also makes the surface more susceptible to arcing. In high voltage systems, electric arcs in PCB can cause the carbonization of the PCB, which can lead to short circuits. Mechanical slots in the suspected areas can be provided to avoid this carbonization.
High voltage PCBs working under high humidity conditions may fail due to CAF (Conductive Anodic Filament) formation. The moisture absorbed by the PCBs, along with the degradation of glass/epoxy bonds, creates an electrochemical pathway. Water acts as an electrolyte, the copper circuitry forms anode-cathode, and the operating voltage creates the potential leading into an electrochemical corrosion process. An effective way to avoid this is by keeping adequate distance between high potential points and choosing a suitable material for manufacturing.
EMI/EMC Compliance
Electro-magnetic interference generated by high voltage systems is higher than low voltage systems, mainly due to radiated and conducted emissions. The electromagnetic wave is generated by high voltage switching in the components like MOSFETs, diodes, inductors, and PCB traces. Parasitic capacitance and inductance on high voltage systems produce sub-harmonic oscillations as well.
The strength of the EMF is directly proportional to the loop area where the high-frequency current is conducted. The higher the voltage, the higher the electric field intensity, which helps the wave travel faster in space. In high voltage systems, as the creepage and clearance distances are higher, the loop area becomes large, leading to increased emissions. Wires and cables act like antennas, and generates significantly higher radiated emissions due to stronger electric field intensity in high voltage systems.
The following design practices can be used to reduce or eliminate the radiated emissions:
- Suitable snubber for MOSFETs and diodes will reduce the high-frequency ringing in the switching nodes.
- The switching loop area shall be as small as possible and unwanted planes; fillings should be avoided in the power routings.
- The interconnecting wires can be twisted in pairs with positive and negative along with protective earth. Hanging wires near the switching circuitry can be avoided.
- Ferrite cores, EMI chokes, and filters can be provided in the design so that the noise coming out of the system is eliminated at the origin.
- In the case of transformers and switching inductors, usage of the shielded components will keep emissions within limits.
Besides radiated emissions, managing conducted emission is also essential for high voltage converters. Conducted emission is the measure of high-frequency noise in the spectrum ranging from 150kHz to 30MHz. It can be reduced by selecting an appropriate input capacitor with low ESR and a parallel combination of electrolytic, film, and ceramic capacitors. Additionally, input filters can be used to attenuate high-frequency noises.
Conclusion
High voltage designs have many advantages compared to low voltage, high current designs. However, one should ensure proper care from designing to manufacturing to reduce the chances of failures in the system. Design guidelines need to be developed and followed to eliminate errors. With the right design, selection of suitable components, maintenance of required creepage and clearances, proper isolation between high voltage points, and adherence to the applicable standards, we can defeat most challenges in high voltage designs.
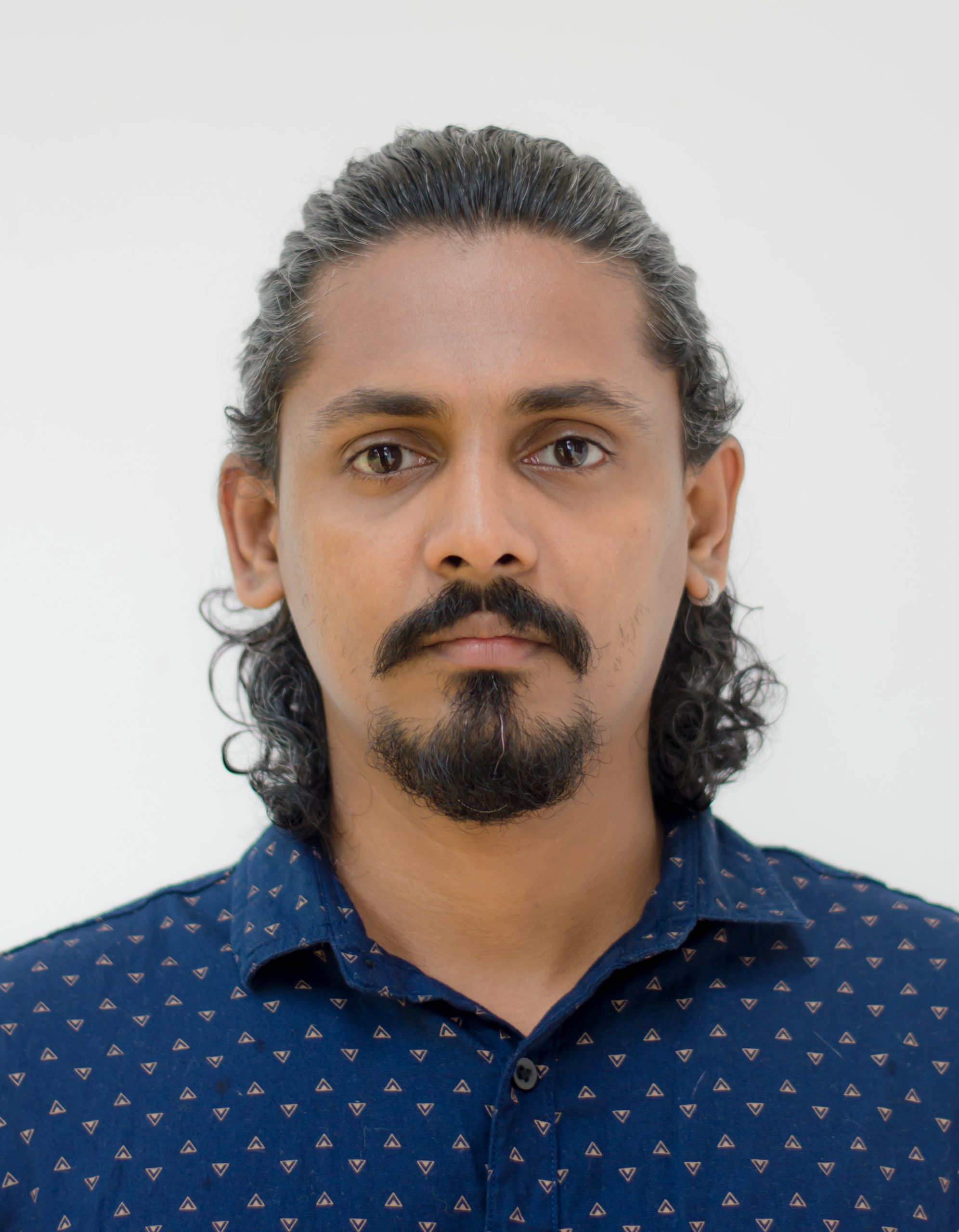
is a Module Lead – Product Engineering Services at Happiest Minds Technologies with experience in Power electronics product life cycle. He has hands on experience in design and development of DC-DC converters, AC-DC convertes and Inverters used in Industrial and consumer applications.
He holds a bachelors degree in Electrical & Electronics engineering and a Masters degree in Power electronics.